The CFM International leap twin spool turbofan is well known for its high- bypass ratio (10-11:1). The CFM International engine is owned equally by two companies – General Electric of the United States and Safran Aircraft Engines of France. This modernized engine is manufactured for the replacement of CFM International CFM56; it’s currently a tough competitor of the Pratt and Whitney PW1000G in the aviation market. The CFM International engine has three variants:
Model | LEAP-1A | LEAP-1B | LEAP-1C |
Fan diameter | 78 in (198 cm) | 69.4 in (176 cm) | 78 in (198 cm) |
Bypass ratio (BPR) | 11:1 | 9:1 | 11:1 |
Thrust | 24,500–32,900 lbf (109–146 kN) | 23,000–28,000 lbf (100–120 kN) | 27,980–30,000 lbf (124.5–133.4 kN) |
Application | Airbus A320neo family | Boeing 737 MAX family | COMAC C919 |
Entry into service | 2 Aug 2016[32] | 2017 (planned) | 2018 (planned) |
(Credits: CFMAeroEngines.com; AviationWeek.com; FlightGlobal.com)
Jean-Paul Ebanga, President and CEO of CFM International, said: “The opportunity to introduce a new engine family into commercial service happens once in a life time for many of us, so this is a very big deal.”
CFM International leap engine has flexible blades which are made from a special resin transfer molding process which prevents blades to twist as the fan’s rotational speed increases. This reduces 500 lbs mass per engine.
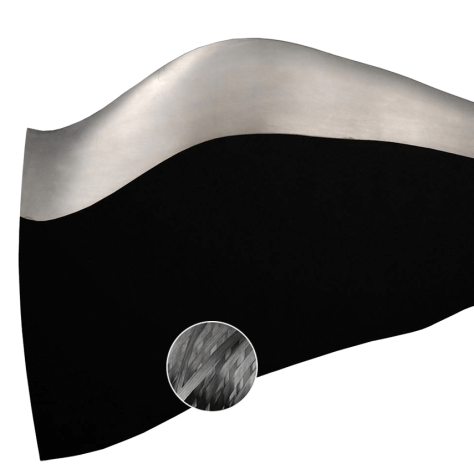
The engine has a single-stage fan, a 3-stage low pressure compressor, and a 22:1 10-stage high pressure compressor. It consists of a two-stage high pressure turbine and seven-stage low pressure turbine. This new engine is efficient with its 40:1 overall pressure ratio.
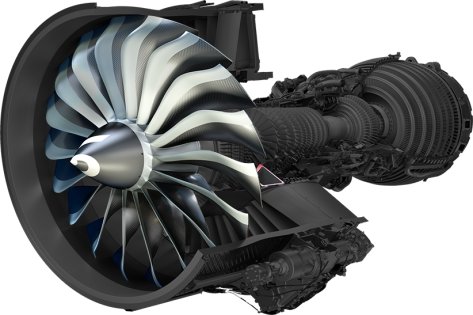
The engine is manufactured with FAA- approved 3D-printed components which makes it lighter and increases the service and reliability. Second generation Twin-Annular, Pre-Mixing Swirler Combustor (TAPS II) reduces the NOx emissions by 50%.
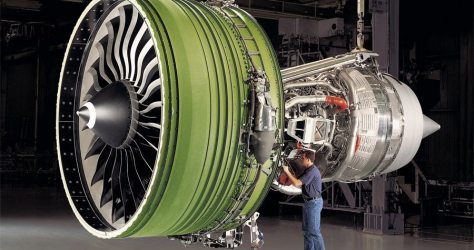
Unlike traditional engines, it pre-mixes the fuel and air to cause lean burn combustion. The leap engine is more efficient than the previous version of CFM56 as it is designed to operate at a higher pressure. GE used ceramic matrix composites to manufacture turbine shrouds.
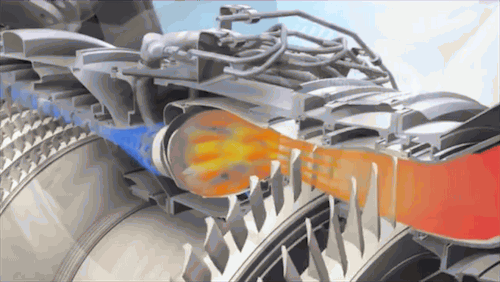
The best debris rejection system prevents erosion by not allowing sand, dirt and other harmful items to enter the core of the engine. This engine has a optimum propulsive and thermal efficiency. The leap engine – 1C is innovated with an O-ring sliding aft thrust reverser which reduces drag and improves the overall efficiency of the engine. The new eductor-based oil cooling systems planted on the inner lining of the fan duct are really reliable. These ameliorations result in 16% lower fuel consumption.

The demand for these new leap engines is increasing day by day. It has attracted more than 5000 orders and GE plans to produce 1700 engines by the end of 2018. This initiative of GE and Safran to produce fuel-efficient engines is getting really successful; both companies are doing remarkable efforts to improve the aviation industry.
(Sources used: CFMAeroEngines.com; AviationWeek.com; FlightGlobal.com)
Featured Image Credit: (CFMAeroEngines.com)